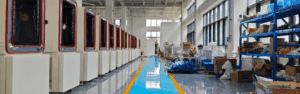
Pitfall 1: Prioritizing Chamber Size While Ignoring Lab Compatibility
Pitfall 2: Believing a “Universal System” Solves Everything
Pitfall 3: Overlooking Future Expansion and System Flexibility
Pitfall 4: Underestimating the Value of After-Sales Service and Maintenance
Pitfall 5: Neglecting Data Management and System Integration
What Do These Pitfalls Really Cost You?
-
Extended testing cycles and delayed product timelines Inaccurate configurations lead to repeated adjustments and slower development.
-
Inconsistent test results and poor data reliability Inadequate control or incomplete data capture compromises test repeatability and credibility.
-
Disorganized lab layout and low space utilization Poorly matched equipment disrupts workflow and resource efficiency.
-
Surging maintenance costs and budget overruns Frequent breakdowns and complex upkeep increase both manpower and financial burdens.
-
Inability to meet future test standards Non-upgradable systems limit your capacity for innovation and scalability.
How to Choose the Right Walk-in Chamber? Three Core Principles
Define a Clear Testing Requirement Profile
Match Equipment to Your Lab’s Physical Conditions
Plan for the Future with Scalable and Integratable Design
Why Choose a DHT® Walk-in Environmental Chamber?
-
Built with German engineering standards and locally manufactured, DHT chambers offer a wide temperature range from -70°C to +80°C and humidity control from 20% to 98% RH. With precise temperature uniformity (±2°C) and fluctuation (≤±0.5°C), they meet the demanding needs of industries such as aerospace, automotive, and new energy.
-
Robust structural design supports on-site assembly and custom expansion (such as integration with vibration tables), improving test versatility. The European-imported touchscreen control system supports real-time data logging, remote monitoring, and fault diagnostics—making operation intuitive and data traceable.
-
Energy efficiency is built-in, thanks to vacuum-insulated windows, eco-friendly refrigerants, and a modular system architecture that reduces operational costs and aligns with green manufacturing goals.
-
With a nationwide service network and flexible customization, DHT® provides rapid response and tailored solutions—cutting costs by 15–20% compared to imported brands, while maintaining CE certification for global market access.
Final Thoughts: Make Smarter Choices, Build Stronger Capabilities
People also ask
What causes inconsistent results in thermal shock testing, even when using a calibrated chamber?
Inconsistent results often stem from hidden thermal gradients within the sample, not chamber malfunction. While the chamber air may stabilize quickly, the internal temperature of dense or complex samples lags behind, causing uneven thermal stress. This can lead to microcracks or solder failure that standard sensors won’t detect. To avoid this, use embedded thermocouples or infrared thermal imaging to monitor core temperatures and adjust transfer timing accordingly.
How often should a thermal shock chamber be calibrated and maintained?
Due to the high-frequency thermal cycling between extreme temperatures, components like sensors, seals, and refrigeration systems degrade over time. It’s recommended to calibrate temperature sensors every 6–12 months and implement a preventive maintenance plan that includes checking seals, cleaning coils, and monitoring system diagnostics. Advanced chambers, like those from DHT®, feature self-diagnostic systems and auto-calibration functions to reduce downtime and ensure long-term reliability.
Can one thermal shock chamber model meet all industry standards (e.g., IEC, MIL-STD, GB/T)?
Not necessarily. While many chambers support a wide temperature range and fast transition speeds, standards like IEC 60068, MIL-STD-883, and GB/T 2423.22 have nuanced differences in transfer time limits, recovery durations, and dwell time requirements. To ensure compliance, select a chamber with programmable profiles and consult the manufacturer (like DHT®) for tailored configuration aligned with your specific certification needs.