Introduction|Les échecs lors des tests ne sont souvent pas dus à un manque de compétences, mais à une sous-estimation de la complexité
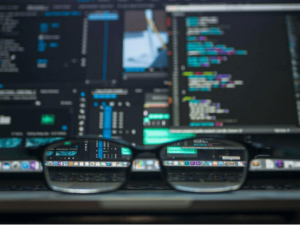
Erreur 1|L’illusion de l’équilibre thermique : les gradients internes sont souvent manqués L'essence des tests de choc thermique réside dans la soumission des échantillons à des changements rapides entre deux zones de température extrême (par exemple, +150°C ↔ -40°C). Beaucoup de laboratoires supposent que tant que la température de la chambre est stable, le test est valide.Mais voici le problème : l'inertie thermique interne d'un échantillon est beaucoup plus élevée que celle de l'air à l'intérieur de la chambre. Pour des assemblages électroniques denses ou des modules de batterie, les retards de température interne causent une accumulation inégale de stress thermique, entraînant des microfissures ou une défaillance des soudures, qui ne seront détectées par aucun capteur de la chambre.
-
Erreur 2|Ignorer l'interaction dynamique entre le flux d'air et la charge thermique de l'échantillon
-
La plupart des chambres de test de choc thermique annoncent des vitesses de transfert dans des conditions sans charge.
Mais dans les tests du monde réel, la capacité thermique et la disposition des échantillons modifient drastiquement l'efficacité de l'échange thermique.
-
Erreur 3|Dérive des capteurs et vieillissement de l'équipement par cycles fréquents
-
Les chambres de choc thermique cycled rapidement entre les zones extrêmes. Au fil du temps, ce stress haute fréquence sur les systèmes internes — réfrigération, chauffage, électrovannes — cause :
-
Dérive des capteurs dans les modules de contrôle de la température ;
Formation de givre dans le système de réfrigérant ;
-
Ces problèmes « mécaniques » peuvent directement compromettre la cohérence des résultats de tests à long terme.
-
Mettez en place un calendrier régulier de calibration des capteurs ;
-
Implémentez une routine de maintenance avec suivi des données et des journaux ;
-
Erreur 4|Mauvaise application des normes et des conditions de test
-
Les normes telles que IEC 60068, MIL-STD 883 et GB/T 2423.22 peuvent sembler similaires — mais elles diffèrent en termes de zones de température, de temps de transfert, et d'exigences de récupération.
-
De nombreuses équipes appliquent des paramètres de test d'après des expériences passées ou des spécifications non liées, ce qui aboutit à des tests qui semblent conformes, mais échouent à la certification ou à l'acceptation par les clients.
Alignez votre test avec les certifications des marchés d'exportation cibles ;
-
Conclusion|Les tests de choc thermique sont un outil stratégique de contrôle des risques — pas seulement une procédure
-
Les échecs aux tests ne ruinent pas seulement un ensemble de données — ils peuvent signifier des rappels de produits entiers, des certifications échouées, ou un dommage durable à la réputation de la marque. Dans les cycles de développement plus rapides d'aujourd'hui et un paysage de conformité plus strict, les tests de choc thermique ne sont pas juste un gardien — ils devraient être un dispositif de protection précoce dans votre processus de conception. En identifiant ces pièges avant même de commencer les tests, vous transformez le choc thermique d'un « point de contrôle réussir/échouer » en une stratégie proactive de qualité qui protège à la fois votre produit et votre marque.
-
Chez DHT®, cette philosophie façonne chaque chambre que nous construisons. Des algorithmes de compensation de l'inertie thermique au contrôle dynamique du flux d'air et aux architectures modulaires qui équilibrent standardisation avec personnalisation — nous allons au-delà des métriques superficielles pour aborder la logique plus profonde et la complexité des environnements de test réels.
Choisir DHT®
Les gens demandent aussi
Pourquoi les résultats des tests de choc thermique montrent-ils souvent des incohérences même lorsque les procédures sont suivies ?
Les incohérences proviennent souvent de gradients de température internes négligés à l'intérieur des échantillons de test. Bien que les lectures de la chambre puissent sembler stables, les matériaux denses comme les batteries ou les circuits imprimés peuvent présenter une réponse thermique retardée, entraînant des stress inégaux et des microfissures. L'utilisation de thermocouples intégrés ou d'imagerie thermique et le développement de courbes d'étalonnage de l'équilibre thermique peuvent aider à atténuer ce problème.
Comment le placement des échantillons affecte-t-il la précision des tests de choc thermique ?
Un placement incorrect de l'échantillon peut perturber le flux d'air et réduire l'efficacité de l'échange thermique, surtout dans les chambres sous charge. Cela conduit à des taux de montée en température réels plus lents et à une exposition au stress incomplète. Pour améliorer la précision, comparez les données de test chargées et déchargées, évitez les zones mortes du flux d'air, et ajustez le moment du transfert pour les échantillons à haute masse.
Quels sont les problèmes de maintenance les plus courants dans les chambres de choc thermique, et comment peuvent-ils être évités ?
Un cyclage fréquent peut entraîner une dérive du capteur, un givrage du système de réfrigération et une dégradation des joints, ce qui réduit la répétabilité des tests. Les solutions préventives incluent l'étalonnage de routine des capteurs, la consignation des données de maintenance et le choix de chambres avec des systèmes d'auto-diagnostic ou d'auto-étalonnage, comme les modèles intelligents de DHT®.